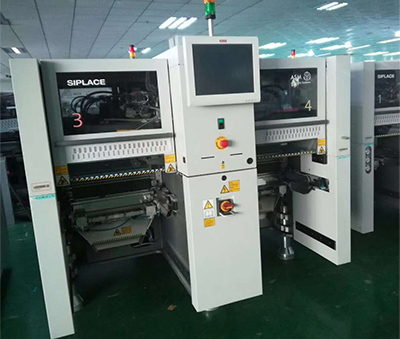
135 1032 1270
Shenzhen Tepu Ke Electronic Equipment Co.,Ltd.
Contact: 135 1032 1270 (Miss Jiang)
Mail box: market@topsmt.com
Address: 201, Building 4, Innovation Port, Hanyu Bay, Fuhai Street, Baoan District, Shenzhen
Siemens high-speed placement machine
Siemens chip placement machines originate from Europe and the United States. European and American equipment has the two characteristics of less use time and good maintenance, so that the equipment can be reused for a longer life, with higher precision and better stability.
The new Siemens placement machine X4 SIPLACE X4 S provides an ideal solution for demanding mass production needs, fully meeting the stringent requirements for flexibility and quality of large-scale manufacturers. The SIPLACE X series features a space-saving, streamlined design, record-breaking speeds, and many other outstanding features and options. Performance is important, but high-speed platforms must also have the flexibility to keep pace with the times. Not only is the SIPLACE X4i S the fastest placement machine on the market today, it also comes with SIPLACE's powerful software, excellent service and innovative applications, making the X-Series the ideal solution for your specific requirements. Outstanding features of the X-Series include support for large thin boards, flexible material setup concept, SIPLACE imaging system, multiple transfer and placement modes, 01005 component placement capabilities, and more. Benefit from features such as lower dpm in the same product category, the fastest new product introduction (NPI) process, and non-disruptive material setup changes. If you have any doubts, we can provide you with a dedicated value analysis to help you discover more about the benefits that the SIPLACE X series can bring to your production floor. At the same time, you are welcome to compare our products with those of other equipment manufacturers. SIPLACE MultiStar: the “all-in-one” placement head
Advantage:
No more bottlenecks, no more head changes required Wider component range and more diverse placement modes for greater flexibility Better overall line performance Most balanced line for better placement performance Innovative technology guarantees quality and reliability using a motor integrated in the placement head frame to drive the star axis and independently controlling each nozzle via a direct motor. Integrated camera system and component sensor. With its revolutionary concept, SIPLACE MultiStar is the world's first placement head that combines different placement modes. You no longer need to change the placement head or configuration, the placement head automatically selects the appropriate placement mode during production. The SIPLACE MultiStar, which just now was placing small and medium-sized components in collect-and-place or mixed mode, can immediately turn the machine into a flexible and powerful end-of-line machine for placement of the next product. SIPLACE MultiStar can handle components from 01005 to 50 x 40 mm. SIPLACE MultiStar can perfectly cope with problems such as product batch miniaturization and product life cycle shortening, and can meet users' requirements for highly flexible and perfectly balanced SMT production lines. With SIPLACE MultiStar you always achieve higher performance with a perfectly balanced production line – no need to change placement heads or perform cumbersome reconfigurations. Especially in the "end of line" area, SIPLACE MultiStar saves time and space and eliminates frequent bottlenecks. SIPLACE SpeedStar Advantages: The world’s fastest placement head Higher placement performance in real-world environments Easily handles 01005 components Best in class quality and reliability Individual angle control unit for each nozzle, integrated camera system and component sensor, all These enable zero-defect placement! The SpeedStar 20 nozzle collection and placement head was developed specifically for the SIPLACE X series of placement machines and is considered the industry standard for speed and accuracy. On the SIPLACE X4i platform, the high-performance SpeedStar can achieve more than 30, 000 cph placement speed! The standard SIPLACE SpeedStar placement head is equipped with a vacuum sensor, a pressure sensor and PCB warpage compensation – features that most other manufacturers only offer as stand-alone options or not at all. Individual component picking, independent angular rotation mechanisms and a digital imaging system that takes individual high-resolution photos of each component ensure the reliable processes required for efficient mass production. So it’s no surprise that it maintains its high level of placement performance when placing 01005 components as small as 0.3 x 0.15 mm. The 20-nozzle collect-and-place head is produced in high volume with high accuracy and can handle components from 01005 to 6 x 6 mm with a maximum height of 4 mm. Despite this speed and accuracy, this placement head and its components are characterized by long life and low maintenance costs – you benefit not only from excellent performance, but also from high availability and low maintenance costs. SIPLACE Imaging Systems: Focus on Manufacturing Quality Determining the location of components and PCBs, assessing component quality, reading barcodes and ink dots, calibrating the system—all these capabilities make the imaging system the most important sensor in a placement machine. With its digital imaging systems, SIPLACE once again sets new standards for equipment manufacturers worldwide. Not just because of each individual component, such as cameras, lighting and software, but also because of the perfect interaction between them. Result: Optical inspection ensures better quality and higher productivity. It is not surprising that it can maintain its high level of placement performance even with 15 mm 01005 components. The 20-nozzle collect-and-place head is produced in high volume with high accuracy and can handle components from 01005 to 6 x 6 mm with a maximum height of 4 mm. Despite this speed and accuracy, this placement head and its components are characterized by long life and low maintenance costs – you benefit not only from excellent performance, but also from high availability and low maintenance costs. SIPLACE Imaging Systems: Focus on Manufacturing Quality Determining the location of components and PCBs, assessing component quality, reading barcodes and ink dots, calibrating the system—all these capabilities make the imaging system the most important sensor in a placement machine. With its digital imaging systems, SIPLACE once again sets new standards for equipment manufacturers worldwide. Not just because of each individual component, such as cameras, lighting and software, but also because of the perfect interaction between them. Result: Optical inspection ensures better quality and higher productivity. It is not surprising that it can maintain its high level of placement performance even with 15 mm 01005 components. The 20-nozzle collect-and-place head is produced in high volume with high accuracy and can handle components from 01005 to 6 x 6 mm with a maximum height of 4 mm. Despite this speed and accuracy, this placement head and its components are characterized by long life and low maintenance costs – you benefit not only from excellent performance, but also from high availability and low maintenance costs. SIPLACE Imaging Systems: Focus on Manufacturing Quality Determining the location of components and PCBs, assessing component quality, reading barcodes and ink dots, calibrating the system—all these capabilities make the imaging system the most important sensor in a placement machine. With its digital imaging systems, SIPLACE once again sets new standards for equipment manufacturers worldwide. Not just because of each individual component, such as cameras, lighting and software, but also because of the perfect interaction between them. Result: Optical inspection ensures better quality and higher productivity.
High-Resolution Digital Imaging SIPLACE imaging systems use superior digital technology in the megapixel range to achieve higher resolution and fast image processing. One image per component Other equipment manufacturers' systems have multiple components capturing an image, often resulting in poor focus. SIPLACE cameras only capture individual components. The system is able to apply its full resolution to a single component without slowing down the placement process. Front lighting makes small areas clearer The SIPLACE imaging system operates with front light because it is far superior to conventional backlight systems. Using front light, this system is able to detect and measure not only component contours, but also the complex surface structures of modern components (BGA, PLCC, etc.). Adjustable Lighting Levels Good lighting is key to image quality. SIPLACE imaging systems therefore use flexible, adjustable lighting levels so that each element is in the right light. High-speed image processing With its powerful algorithm, the SIPLACE imaging system can measure and analyze each component in just a few milliseconds, ensuring higher speed and better placement quality. For quality control purposes, the system can store 500 pictures of defective components. Special sensors For additional support, SIPLACE also offers special sensors. For example, the coplanarity module uses laser detection of pin warpage to check the coplanarity of large components to avoid poor soldering. SIPLACE X Feeder The intelligent SIPLACE X feeder provides a highly flexible basis for innovative setup concepts. Thanks to their hot-swappable functionality, they enable quick and easy loading changeovers – without having to stop the machine.
Advantages: Wireless power and data transmission (EDIF) Brushless DC motor self-adjusting pick-up position 8mm X feeder Ease of use: Single track feeder module Color LED displays feeder operating status (online, Offline, etc.) Menu-driven LCD panel displays the current status of the feeder (track, sequence, etc.) Flexibility: Adjustable sequence Adjustable feed speed Built-in program automatic update capability Conveys 25 mm high components Handling short tape function Built-in 01005 function Adjustable tension Built-in PSA (sticky tape film) processing function Intelligent: All SIPLACE X feeder modules can be equipped with splicing sensors Each SIPLACE X feeder has an ID and is suitable for loading confirmation The flexible SIPLACE production concept automatically sets all production-relevant parameters such as sequence and feed speed when incorporated into the traceability system solution.
Flexible product concepts for any need
Shenzhen Topco Electronic Equipment Co., Ltd. specializes in providing the following SMT equipment to electronic manufacturers:
MPM printing press , Koh Young SPI
Panasonic placement machine , Fuji placement machine , Siemens placement machine
Meilu AOI , Vitronics Soltec reflow soldering
The entire SMT production line equipment, as well as spare parts, services and solutions.
135 1032 1270
Contact: Miss Jiang
Mail box: market@topsmt.com
Address: 201, Building 4, Innovation Port, Hanyu Bay, Fuhai Street, Baoan District, Shenzhen
Please submit your request and we will call you right back