feature:
Process alignment capability 2 Cpk @ ± 20μm 6-Sigma
Device alignment capability 2 Cpk @ ± 12.5μm 6-Sigma
8 seconds print cycle time
HawkEye® 1700 Post-Printing Inspection
DEK Instinctiv™ V9 user interface including real-time feedback, online help and error fixes
ISCAN Intelligent Scalable Control Area Network
Semi-automatic stencil loading
Ability to handle standard size boards; larger 508mm×508mm
Color TFT touch screen, keyboard and trackball
advantage:
Standard support fixture table
Fixed steel mesh clamping system
Fast, easy and stable bus-based control of the intercom system provides responsive and intelligent equipment control.
DEK Instinctiv™ V9 makes setup faster, shorter makeready time, less operator training required, and easier avoidance of errors
Accepts all industry size steel mesh, using VectorGuard®, product conversion is faster
Rapid product changeover and rapid redistribution when business needs arise
Maximize manufacturing output with productivity tools focused on enhancing yield and speed potential
PROACTIV printing technology--revolutionary printing technology
This breakthrough process technology from DEK enables hybrid assembly of next-generation and standard components using a uniform thickness of stencil using traditional printing processes.
Although the screen printing process involves many aspects, the screen opening area ratio is the key to determining whether to print or not. In order to cope with miniaturized components and hybrid assemblies, the opening area of the stencil is reduced, and the chance of obtaining a successful printing effect is also reduced. Current area ratio process rules limit the ability of traditional printing processes to handle smaller screen openings, but ProActiv breaks through and redefines these rules.
ProActiv expands the process window to enable small-aperture printing of 0.3mm CSP components and 01005 passive components. After activation, ProActiv will enhance the activity of the solder paste in contact with the squeegee. There is a unique action here that instantly makes the solder paste more compatible without changing its properties. The process improves aperture filling, thereby changing solder paste transfer efficiency, directly improving quality, yield and throughput – including today’s sub-assemblies.
ProActiv provides a stable and robust process that significantly increases yield and reduces rework and scrap. It also reduces the frequency of screen cleaning to increase production throughput, and extends the life of the screen and scraper by reducing friction between the scraper blade and the screen. The result is significantly reduced production costs and unparalleled solder paste transfer efficiency
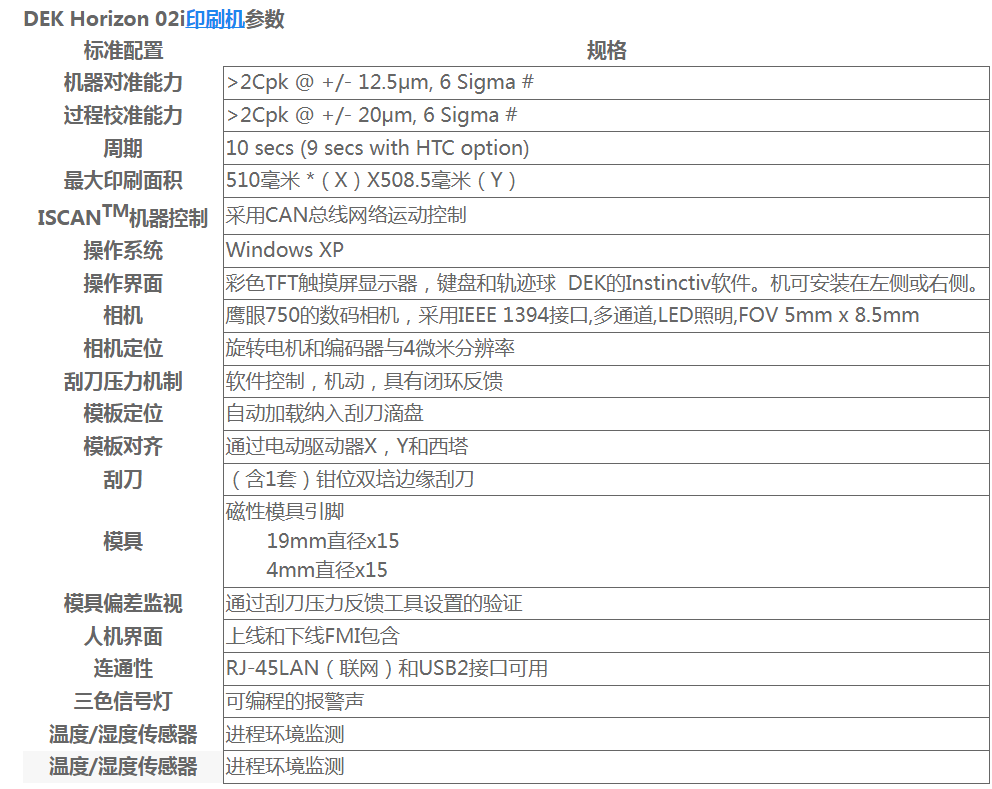
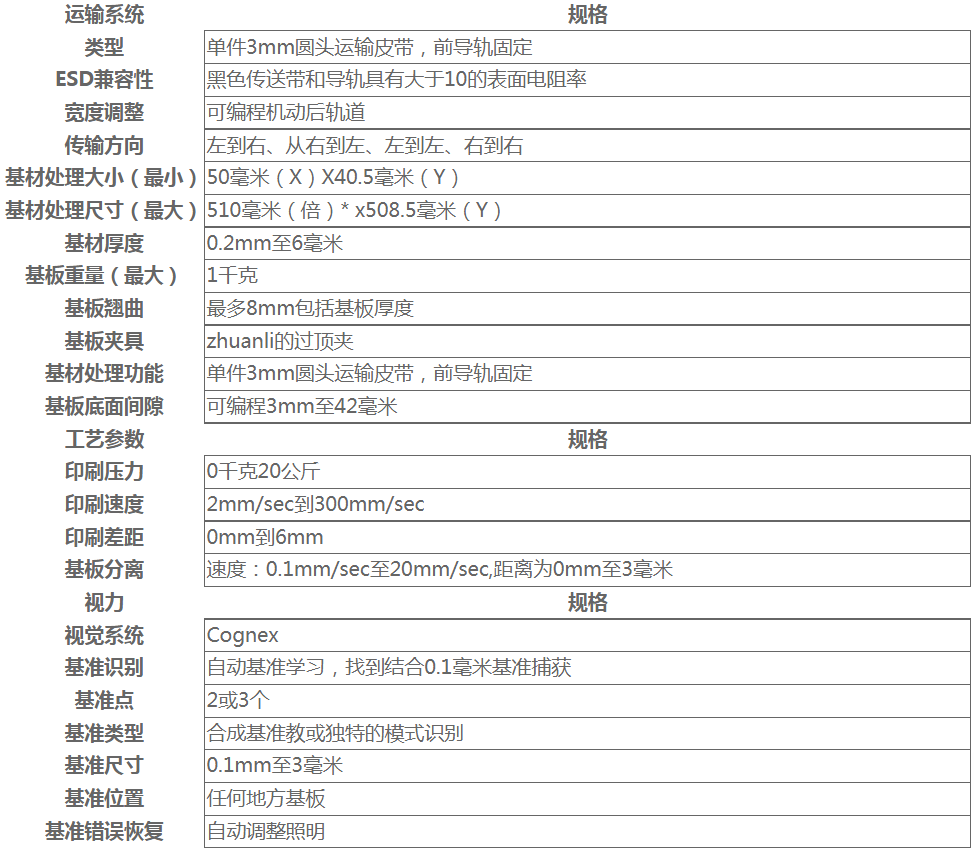
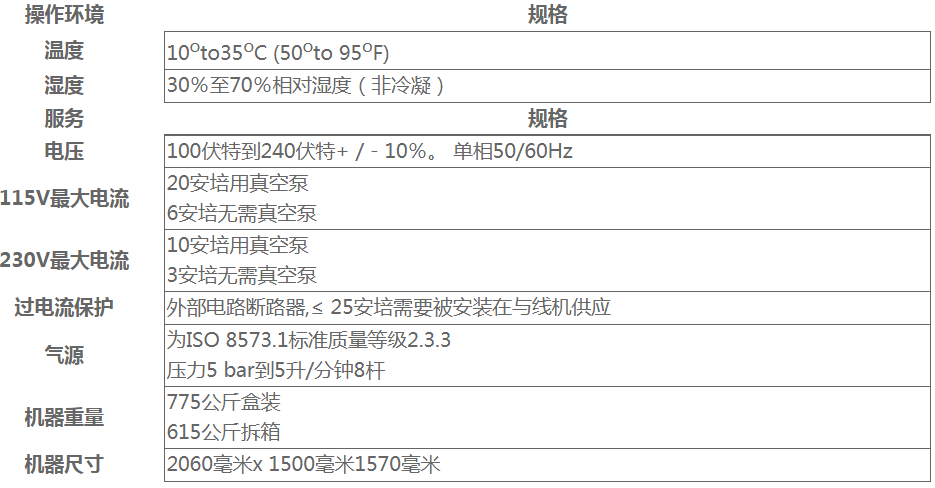
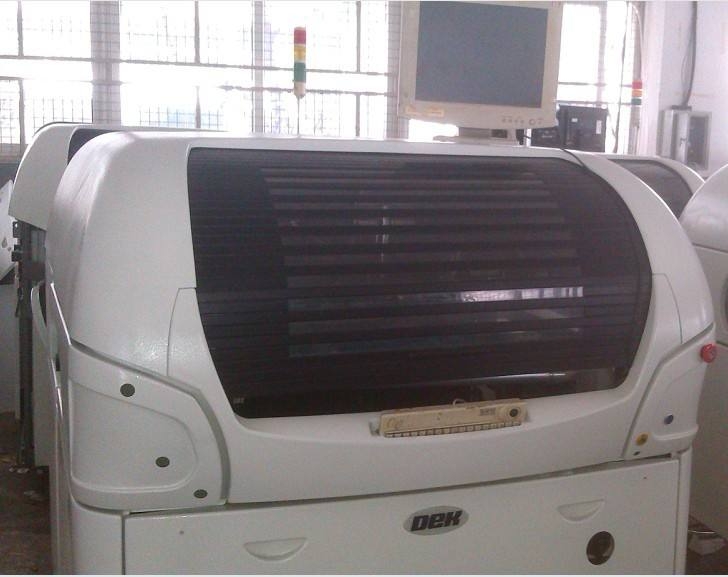